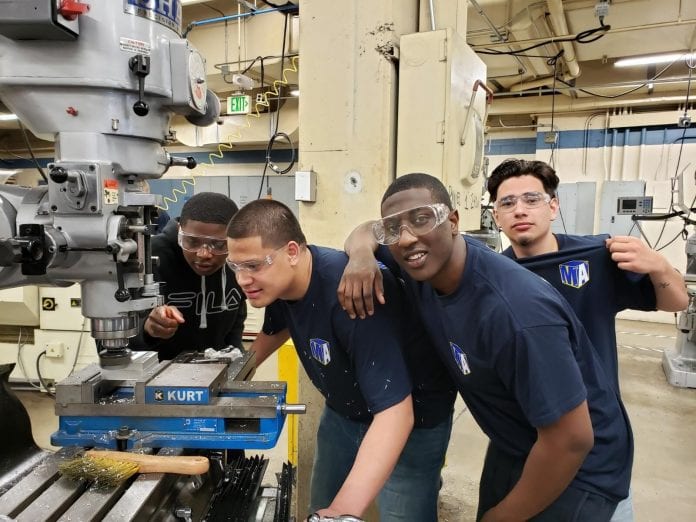
In early summer 2019, the leadership team at Berry Global called a meeting with every staff member at their Tacoma plant. The company was preparing to bring in six youth to serve in a pre-apprenticeship program and they wanted to give their employees a chance to ask questions. The reason: all six were involved in the juvenile justice system and were currently serving time. For 12 weeks, the staff would be serving as trainers and mentors.
“We wanted our employees to have the opportunity to voice any concerns,” says Jackie Johnson, Quality Assurance and Human Resources Manager. “We encouraged them to give these youth a chance to be a benefit to the community.”
Now, as the apprenticeship period is winding down, the staff has another question. How soon can they get more from the same program? “This was a good group of young people,” says Johnson. “The minute they came in, everybody was excited to have them here. Now everyone, even the tenured employees, is asking how soon we can get another.”
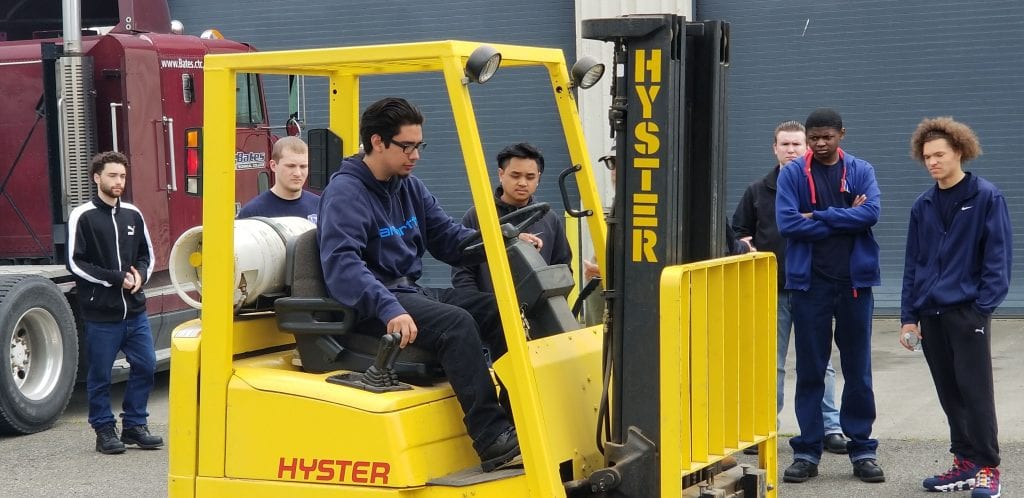
The apprenticeship was the end result of a more than year-long collaboration between six different agencies: Pacific Mountain Workforce Development Council (PacMtn), Aerospace Joint Apprenticeship Committee (AJAC), the Department of Juvenile Rehabilitation, the Division of Vocational Rehabilitation, ResCare and Bates Technical College.
Over the course of a year, staff from PacMtn’s My Journey Out Beyond (MyJOB) program worked with youth at Echo Glen Children’s Center, Naselle Youth Camp and Green Hill School juvenile detention centers, providing workplace readiness skills, mentoring and work-based learning. Once it was complete, they put together a cohort of 10 students from the three facilities based on interviews and career assessments as well as expressed interest in manufacturing. Those 10 students moved into the Oakridge Community Facility in Lakewood and embarked on a 12-week AJAC pre-apprenticeship training called Manufacturing Academy.
The program, housed at Bates Technical College, includes 32 college credits, an OSHA 10 certification, CPR and first aid training, and a Lean Manufacturing certification. “It gives a really good in-depth look at all the different career tracks in manufacturing they could go into,” says Briana Durham, Director of Youth Apprenticeship at AJAC. “They learn a bit about manual machines, riveting and blueprints, welding and lean manufacturing principles. Then we brush them up on math skills and precision measuring, those entry-level skills that employers in the region are looking for.”
The next step was finding the youth a place to practice their newfound skills. That’s when ResCare stepped in, supported by funding from PacMtn, to act as case managers and find an appropriate company. “We searched for a place where we could get them the experience of what real work would be like,” says Will Yeager, Project Director at ResCare Career Services. “We targeted manufacturing.”
On their end, Berry Global was contending with an impending workforce shortage. “We currently have an average tenure of 20 years at our facility,” says Johnson. “We have a number of employees who are looking to retire and finding replacements can be challenging in the manufacturing business. We were looking at our options.”
Berry Global agreed to take the majority of the youth enrolled in the pre-apprenticeship program. Starting at the end of July, six of them worked three days a week the plant, rotating through the maintenance, quality assurance and packing departments among others. PacMtn provides a stipend for the work they do and ResCare functions as the employer of record, meaning they assume liability in the event of any mishaps.
The program has been a success according to Jage Curl, Associate Director of Youth, Equity and Special Populations at PacMtn. “We went to the facility and saw that Berry Global was doing an amazing job with each one of the youths. Some were doing quality assurance, some were operating forklifts, and some were packing and using different machines. We got to see the youth be incredibly proud of the work they’re doing.”
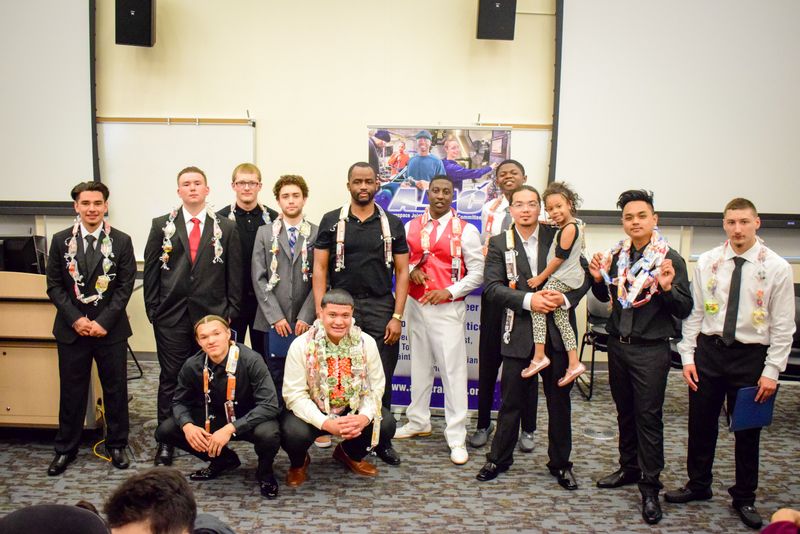
Jacob Perry originally enrolled in the program as a way to move into a more comfortable facility, but now his perspective has changed. “Once I started the program and met the instructors, I enjoyed it,” he says. “I’ve learned a lot of job skills.” He credits MyJOB with preparing him for how to show up at a workplace. “They trained us for almost any scenario.”
Aside from practical skills, My JOB addressed less tangible aspects of workplace life, says Jaylen Lilly, another participant. “I learned how to respect someone else’s culture,” he says. “Right now, I’m working with people from a lot of different places and the program taught me how to bypass the biases in my head.”
Once the pre-apprenticeship at Berry Global ends in September, Lilly and Perry will be eligible for a full apprenticeship. That’s the point, says Durham. “The whole goal is to get them into adult apprenticeships so that when they get released, we get them into more permanent jobs,” she explains.
But first, if Johnson has her way, the partners will come together to acknowledge the program and its participants. “Our leadership have agreed that we need to celebrate these young people,” she says. “We’re looking to have some refreshments and invite their families to come, see what they’ve been a part of and celebrate their accomplishments.”
For more information about PacMtn’s My JOB program, visit their website.